Featured Article
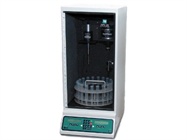
Please check out our Homogenizing Systems section for more information or to find manufacturers that sell these products.
The act of homogenizing can mean the act of blending, mixing, disrupting, emulsifying, dispersing, or stirring. The method used by homogenizers to accomplish any of the above tasks can be categorized into three major methods: ultrasonic, mechanical, and pressure. The governing principles of each method will be outlined in this article, along with key purchasing considerations such as specifications, validation, and price point analysis.
Homogenizers background and features
Homogenization is a common and important sample preparation step preceding the analysis of nucleic acids, proteins, cells, pathogens, and other samples both in the research and industrial laboratory settings. Understanding the commercially available homogenizing methods can make selecting the right homogenizer for a particular application easier.
Ultrasonic homogenizers rely on the intense shear forces combined with the high local temperatures and pressures generated by acoustic cavitation. During acoustic cavitation, microbubbles grow and merge until reaching resonant size and then collapse, creating a shock wave and eddy with enough energy to disrupt cells.
Three common mechanical homogenizers are commercially available: bead mills, rotor-stator, and blade. By vigorously agitating grinding media (i.e., steel, ceramic, and/or glass) and sample within a sealed vial or titer plate, bead mills are a preferred method to disrupt microorganisms, plant, or animal tissue. Careful control of the crushing action generated by the grinding media can be achieved by bead mills, creating a versatile homogenizing solution from the delicate, or low shearing of nucleic acids to disruption of yeast, fungi, or robust bacteria and microalgae. Additionally, the grinding media and vials are disposable, thereby avoiding cross-contamination between samples.
Rotor-stator homogenizers are well-suited for plant and animal tissue. Similar to ultrasonic methods, rotor-stator (and blade) use cavitation, but also mechanical shearing of the sample. Blade homogenizers, commonly known as blenders, consist of either a bottom- or top-driven cutting blades suitable for producing extracts from plant and animal tissue.
Forcing a mixture, such as a cell suspension, through a very narrow channel under pressure creates massive pressure drops, focused turbulent eddies, and strong shear forces. Some pressure homogenizers may include an impact ring with which the suspension will collide. Alternatively, some pressure homogenizers will direct multiple high-velocity streams of suspension into one another. Instruments that include such impingement designs are generally more effective.
Table 1 - Homogenizer manufacturers and distributors
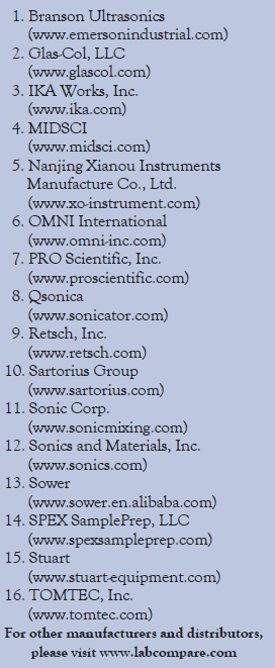
Key purchasing considerations for homogenizers
Once the application has been matched to the homogenizing method, choosing the right homogenizer manufacturer, such as the selected manufacturers listed in Table 1, can be difficult. To aid the buyer in understanding homogenizer requirements, common homogenizer specifications and terms are defined below along with their respective implications.
1. Motor size (Watts): The requirements of the motor size, generally measured in power or Watts, are application specific. “There is no need for overkill—If you are processing small microvolumes, a lightweight, handheld unit will most likely be ideal,” explained Holly Yacko-Archibald, Sales Director at PRO Scientific Inc. (Oxford, CT). “On the opposite side of the statement, if you are processing a thick, viscous material and realize that you are going to put more strain on the motor [then] you may need a higher wattage unit like a benchtop unit.”
2. Speed control and range (rpm): Speed control is a common feature on multiple types of homogenizers, though most samples do not require the maximum speeds found on many of the homogenizers on the market. For mechanical homogenizers, “it is best to start off slow and gradually increase speed, [and] make sure you are in control at all times. If precise control within a few RPMs is needed then you might want to consider a unit that provides an optional external speed control box,” suggested Yacko- Archibald. Bruce Green, Manager of Technical Support with Sonics and Materials, Inc. (Newtown, CT), provided some insight on what speed control means for ultrasonic homogenizers, “The ‘user control’ of an ultrasonic generator is to vary the amplitude of the probe, which is the amount of incursion of the probe into the liquid, thus causing the vibrating probe face to act upon the liquid with greater or lessor force.”
3. Processing range (mL): This parameter refers to the volume, or sample size, to be homogenized. It is possible that multiple sample sizes, from microliters to thousands of liters, can be processed using the same homogenizer unit. However, you will need to purchase the appropriate generator, probe, or tool to match the volume range. When asked to comment on the processing range specification, Yacko-Archibald replied, “What generator/probe will give you the most ideal homogenizing at a micro/mL range will not be the same generator/ probe that would be best for processing multi-liters of sample at once.” Green added, “The size of the individual probe can be varied to handle specific volumes of process liquids, thereby creating a very efficient use of energy.”
4. Sound level (dB): Managing the noise generated by equipment can improve the overall efficiency and environment of the laboratory. “In ultrasonic [homogenizers], the term refers to any frequency above the common threshold of human hearing, usually noted at 18 kHz, thus any ‘noise’ that is created is not a result of the ultrasonics itself, but the result of the vibration of the liquid making noise and is different for vessels of varying materials,” explained Green.
5. Weight and dimensions (kg, mm): The weight and footprint of the homogenizer unit can vary greatly and is generally determined by the application, and/or the available space where the homogenizer is to be used. Handheld units can weigh as little as 10 oz. (i.e., the Omni THQ [Omni International, Kennesaw, GA]), while heavy-duty industrial benchtop models may weigh multiple pounds.
Validation
Once the buyer’s needs are well understood, identify a suitable homogenizer manufacturer and the necessary components. To assure the end user of a product’s ability to achieve the performance outlined by the manufacturer, a validation should be performed prior to placing the homogenizer in use. Request a demonstration from the manufacturer and consult with other laboratories with similar homogenizer needs. When repeatability is paramount, Bruce Green provides the following advice: “In liquid processing using an ultrasonic system, watts of energy can be easily identified and measured, thereby creating a repeatable and verifiable protocol identity, important for critical experimentation and test validation.”
Important price points for homogenizers
As with many types of laboratory equipment, buyers should not necessarily be swayed by the initial cost of the homogenizer. “Again, it is essential to keep in mind that one of the most important components in homogenizing is the generator/ probe and not necessarily the motor unit,” said Holly Yacko-Archibald. “The most expensive item in homogenizing will be the generator/probe. However, if properly cared for and regularly maintained, the investment you make today can last for decades.” Additionally, recurring cost for the disposable grinding media and vials needed for bead mills may exceed the need to minimize cross-contamination.
Conclusion
Because the probe is the only part of many homogenizers that is in contact with your sample, the probe itself may be the most important consideration when purchasing a homogenizer. “With that in mind, make certain you are buying something that is easy to take apart and clean, manufactured out of a high-quality material (such as 316SS), carries a strong warranty, and has replacement parts available,” concluded Holly Yacko-Archibald. “By investing in and properly caring for (and) maintaining a good homogenizer and generator probe they will last for many, many years!”
Additional purchasing considerations include the reputation of the manufacturer itself. Nonproduct issues must be evaluated in addition to technical needs. These include the industry knowledge and depth of experience of the company.
T. Keith Brock, BS, is a Contributing Writer, American Laboratory/Labcompare; e-mail: [email protected]. The author would like to thank Holly Yacko-Archibald, Sales Director at PRO Scientific Inc. (Oxford, CT); Bruce Green, Manager of Technical Support, Sonics and Materials, Inc. (Newtown, CT); and Tim Osborn-Jones, Director Sales & Marketing, SPEX SamplePrep LLC (Metuchen, NJ), for their contributions to this article.