Featured Article
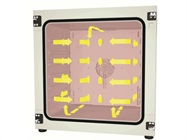
Microbiological incubators are temperature-controlled ovens that operate within the range of 5–70 °C, providing stable, precise conditions for growing cell cultures. These units find application within biotechnology, genetic engineering, brewery, food, pharmaceutical, and other labs.
Before purchasing a microbiological incubator, consider what is being tested. How delicate are cultures of yeast, bacteria, fungi, anaerobes, and aerobes? Should temperature mapping (required whenever regulatory-controlled product is being manufactured) be performed prior to onset of testing? Do extra steps need to be taken to eliminate particle contamination? What are the testing parameters? Should a shaker be added to your testing equipment? Are there limitations on the test matter? Any stabilization protocols that need to be considered? Are there additional research options? Incubators can be used for additional studies, but recalibration at the set temperature as well as additional qualifications should be performed to ensure validity for the tests performed. Consult manufacturer information to determine incubator parameters for temperature accuracy, stability, and uniformity, and consider how this relates to sample requirements.
When samples are received, care must be taken to ensure proper handling. Samples should be logged and handled safely. Contamination risk can be minimized by training lab personnel in proper handling methods as stipulated by GLP and various ISO documents for quality of tests. In addition, specific unit calibration for temperature uniformity on various positions on each shelf and in the shelf space will assure specification validity for each sample placement.
There are two convection options for incubators—gravity convection and forced or mechanical convection. Gravity convection enables closed, continuous operation, and is suitable for gentle incubation of organisms and conditioning of heat-sensitive media. Forced or mechanical convection is well-suited for more demanding tasks that include large batches and full loads, and provides adjustable airflow with high temperature uniformity and quick recovery time (see Figures 1 and 2).
Refrigerated incubators are available with either compressor or thermoelectric (Peltier) refrigeration. Models with compressors have better heat compensation and lower minimum temperatures and are more energy-efficient. Thermoelectric incubators are smaller, lighter, and have low vibrations, and thus run more smoothly and are cost-effective. In addition, thermoelectric units have more complex programming options and provide reproducible results.
Incubators are available in a variety of sizes, from tabletop to larger, high-performance units. A survey of the lab space will determine whether one incubator is sufficient. Stackable units can save valuable floor space. Carts with locking wheels provide mobility when needed and safety in use. Heavier vessels or larger samples may necessitate a reinforced inner chamber.
Most units have an interior glass door to enable product inspection while minimizing contamination risk. Shelf size should be ample to accommodate samples and larger vessels or equipment. Some tests require a corrosion-resistant interior; if so, it is best to discuss this with vendors.
Interior lighting is a useful option: while bacteria and fungi are easy to detect inside an incubator, mycoplasma and other organisms can be more difficult to identify, a task made easier by interior lighting.
Incubators need to be decontaminated on a regular basis. Determine whether disinfection or complete sterilization is preferred for the samples and processes for which the unit is used. Regular cleaning is also required; though it will be made easier by following regular disinfection and/or sterilization routines, it is still important to maintaining a healthy incubation environment. Some models offer HEPA filters, which are used to remove very fine particulates from incoming air. Because they capture and retain potential contaminants, cleaning these filters should be part of SOP. Aseptic techniques should be used at all times to reduce the risk of microbial contamination.
Awareness of unit cool-down duration can allow cleaning to be scheduled after return to ambient temperature. Access ports can be installed to monitor an incubator’s internal temperature. If desired, probes can be positioned inside the unit, but should not be connected through the door gasket as this disturbs the seal, potentially leading to heat loss and compromised performance. An internal socket can be invaluable as it can power a shaker, mixer, or other devices.
Some incubators can be programmed to turn on and heat up prior to arrival of lab staff. Independent temperature safety devices monitor a unit’s interior temperature and provide visual or audible alarms if changes are sensed. Door locks can restrict access for specific testing. Many incubators are equipped with intuitive, user-friendly programming, some with touchscreens. Some user interfaces offer multilingual displays, customizable displays, and data logging via a USB device or links directly to a lab computer for analysis.
Best practices and results
Standard validation practices of installation qualification, operational qualification, and performance qualification are critical to obtaining the best results. Unit calibration should be done at operating temperature to ensure proper performance and reproducible results. Validation should be performed at regular intervals to maintain the incubator’s effectiveness. If the unit is out of calibration, temperature mapping can be done using a calibrated NIST traceable measuring device to ensure that the acceptable criteria variation is followed. An outside agency can provide yearly calibration of the unit.
Examples of common problems and solutions
The following real-life examples provide clear indication of why conforming to SOP and GLP practices will provide long-term benefits and increase productivity.
Problem 1
An incubator was reported to be experiencing phases in which it alternately provided good and bad data. The user performed an analysis to try to determine the cause of the cyclical bad data, and found that GLP was not being followed. Lab technologists were performing the tests over the specified time but, due to the complexity of the testing, time was not scheduled to disinfect the incubator at regular intervals.
Solution
Processes and procedures for running tests and research must be reviewed for time cycles and leave appropriate time for cleaning and maintenance. When planned within GLP and GMP, results should be more conclusive.
Problem 2
Stem cell culture protocol requires reduction of aerial contamination. How can this be done?
Solution
Incubators have optional HEPA filtration for airborne particle removal within the unit. Another solution is to set up a cleanroom-type lab with specific aseptic procedures in place for sample processing and monitoring, as well as GLP to eliminate as much contamination as possible.
Problem 3
A laboratory reported that its incubator was not performing to the standards expected. The temperature values were off. Evaluation showed that the incubator was not placed in an optimal location.
Solution
Incubators should be located in a temperature-controlled, stable area—away from doors, windows, air conditioning, or heating ventilation. The ideal location is in near-cleanroom conditions to ensure the best performance.
Nancy Klimpel is marketing communications manager, BINDER Inc., 545-3 Johnson Ave., Bohemia, N.Y. 11716, U.S.A.; tel.: 631-224-4340, ext. 123; e-mail: [email protected]; www.binder-world.us