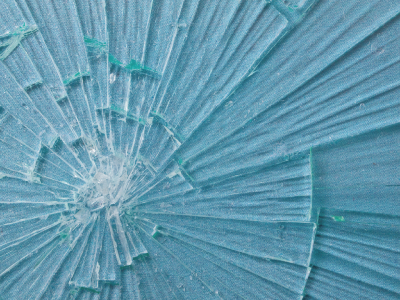
EPFL researchers have captured 3D images of how brittle materials crack, providing important information for use in composite material construction. The findings reveal not only how cracks form and move, but also the energy required to drive those cracks.
Traditional approaches to crack analysis assume that cracks are planar, or formed on the 2D surface of a material. While this is true in many materials, common everyday brittle materials such as glass often propagate into three-dimensional networks comprised of complex features and ridges. Observing this complexity in real time has proven challenging due in part to the speed at which these cracks form.
In the study, published in Nature Physics, the team utilized confocal microscopy and a simple Swiss Army Knife to observe the cracks, unveiling a positive correlation between the material toughness and the complexity of the cracks formed.
“The energy required to drive cracks has traditionally been considered a material property, but our work yields unique insights into the key role of geometry: namely, that by increasing the complexity of geometric features at the crack tip, a material can be made effectively tougher, because more strain energy is required to advance a complex crack than a simple one,” said John Kolinski. “This highlights an important gap in the current theory for 3D cracks.”
The method employed relied on creating thin slices of four hydrogels as well as an elastomer to serve as a proxy for glass and brittle plastics and materials such as rubber respectively. These proxies allowed the team to observe and measure deformation without shattering. During testing the team found that the scissors of the Swiss Army Knife created geometrically complex cracks in the hydrogel samples. The team assembled a three-dimensional map of the fracture surface by capturing and stacking a series of fluorescent images obtained from the confocal microscope.
“People have long known that cracks can become complex by looking at fracture surfaces after the fact, but what is lost is the understanding of the loading conditions when the crack emerged, or what forces the sample was exposed to,” siad Kolinski. “Our innovative imaging method has made it possible to characterize this relationship rigorously in-situ.”
The findings of the study suggest that as the geometric complexity of the crack increases, additional strain energy is required to drive it.
“The fact that we can isolate how geometric complexity emerges with such an inhomogeneity in the material could motivate new design approaches,” said Kolinski. “Our work also highlights the importance of care in carrying out materials testing, as we now know that any geometric deviation from a planar crack front may lead to a mis-measurement – and potentially dangerous over-estimation – of material toughness.”