by Grayson Dance, Relocation Services Product Manager, Agilent Technologies, Inc.
The need to relocate a lab can range from circumstances that include the requirement for temporary social distancing measures, making space for new instrumentation, or even new site construction and acquisitions. Relocating and moving a lab is a significant project and can be one of the most critical and impactful physical changes a lab can make.
Lab productivity depends on maximized instrument uptime, so the challenge in moving a lab becomes one of physically moving the lab and moving it so the instrument ‘utilization and science’ stay as continuous as possible. A day of downtime can potentially cost a lab many thousands of dollars, so prolonged downtime can add up quickly.
But how do you minimize downtime from an inherently disruptive process? Consider enlisting the services of a lab move partner who understands the complexities of a science-ready move. A partner who understands the complete end-to-end process for moving everything in a lab, focusing not just on transportation, but also on a faster return to science. A science-ready move gets the lab back up to speed sooner by proactively eliminating causes of downtime that can occur before, during, and especially after a move. Easy to miss details such as utilities or computer networking can cost days of downtime to fix for a single asset, and that cost only grows when moving more equipment. Avoiding prolonged downtime requires more than just attention to detail – pre-move planning, risk mitigation, contingency plans, and more are all considerations.
This article explores an increasingly popular option, using an industry partner to help with the move. The decision and choice of a suitable industry partner who is experienced and prepared to deliver is critical, as the smallest missed detail can disrupt a swift and seamless return to operations. Ideally, an industry partner with scientific familiarity would be the best choice, one who could combine lab workflow expertise with the move, and project management experience to successfully manage such a move. So how does such a science-ready move happen? With an industry partner onboard, it starts with a solid plan, who to coordinate with, what needs to move, where the lab is moving to, when the lab needs to move, and how to make it all happen smoothly.
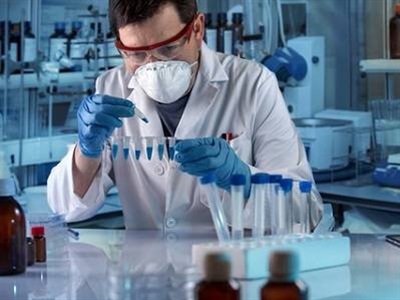
Planning the move with a focus on the science
Scheduling: With a science-ready move, every part of the move needs to focus on the goal of returning to science as quickly as possible. This focus is critical in the planning stage. Ideally, the move would be meticulously planned around the lab’s intricate economics, long before any boxes are packed. The further in advance, this plan can be developed, the better, as this provides all suppliers the time to allocate necessary resources for the project. Proper resourcing can prevent weeks of unnecessary downtime by consolidating the work to the move timeframe and avoiding unnecessary follow-up service calls that could prolong disruption. Considerations should include current projects, availability of shared-use spaces, and other time-sensitive aspects. Each of these elements should factor into the plan to avoid any potential delays.
Often when it comes to scheduling, lab moves are coordinated to happen all at one time, halting all operations for the duration of the move. An experienced industry partner can manage the move via phased moves to minimize the disruption to lab operations. A phased move ensures that relocation of one subset of equipment doesn’t affect the operation of another, meaning equipment stays functional as long as possible. This is especially helpful in situations such as multiple labs consolidating to a single space, equipment from one space being dispersed to multiple destinations, and when a lab cannot pause operations at the same time.
Inventory: Another challenge in developing a move plan is understanding the scope – how much there is to move. Similar to moving to a new house, labs usually have more that requires moving than expected. An industry partner will inventory all items in the lab. From mass spectrometers to mousepads, knowing what needs to be moved helps avoid surprises and can also provide an opportunity for cost savings. An industry partner will analyze the itemized list to determine if everything should really be moved. In some instances, buy-back services may make more sense. For example, an older instrument could be traded in, avoiding the need to pay to relocate it. The trade-in credit could be applied to either the move or to the purchase of a new instrument. Liquidation opportunities can also help in some circumstances. What is left behind can potentially be sold. The industry partner can assist with locating buyers for the equipment. Once relocated at the new site, an experienced industry partner will probably have a technology refresh service that can help adapt data and staff to the new setup for a quicker and more efficient startup time.
Risk assessment: A rigorous pre-move risk assessment is the best way to avoid surprises on moving day. A thorough evaluation can identify any potential obstacles, and the best plan will include contingency plans for each potential obstacle. From weather to shared-use elevators to a pandemic, every possible scenario would be factored. An experienced industry partner will have project managers who are adept and know what to look out for. Will the equipment fit through all the doorways at the new site? Is the elevator big enough? Such attention extends across the breadth of the move from start to finish at the new destination. An industry partner with a science-ready mindset would be uniquely positioned to create the ideal space in the new location. They work with contractors to build the areas around the lab’s needs including ensuring that power supplies are correct for incoming instruments and that the utilities are in the right places. They will also ensure that all assets physically fit into the new space. Incorporating these considerations into the initial planning and design of the new space will eliminate any issues on move day which could lead to days of downtime waiting for the problems to be resolved.
Ideal partner: The perfect industry partner works with the lab to determine the right team to ensure a successful move. This approach guarantees expert service for both the equipment and the logistics. An experienced industry partner can also bring together the resources required to relocate multiple vendor equipment, via coordination with other industry partners. That additional industry partner may be an OEM for the more specialized lab equipment, a broader third-party service provider for less complex pieces of equipment, or more often, a combination of both. Large moves can involve many moving parts, so having an experienced partner to facilitate removes a lot of the stress of a science-ready move.
Move-adjacent services
A science-ready move provides the highest level of continuity in lab operations. Some industry partners also offer move-adjacent services that make sure the new space is as functional as it can be, as quickly as it can be. Some of these services may include:
• Compliance services for guaranteed regulatory compliance further ease the transition to a new space.
• Program management to handle instrument service and lab operations to improve operational continuity.
• Inventory services let you know what you have and help eliminate the time-consuming step of taking inventory.
When circumstances call for a science-ready move, ensuring the right team is in place is critical. Planning through careful attention to timing, scope, and potential risks will negate much of the risk. Enlisting the services of an industry partner who brings lab expertise, move experience, and the network of services to fill any gaps will avoid delays, save time, and get the lab back to business sooner.
About the author: Grayson Dance has held multiple positions focused on exploring the challenges of modern research laboratories and advancing those laboratories' operations. He holds a degree in English from Trevecca Nazarene University in Nashville, Tennessee. Grayson joined Agilent in 2016, and took on the role of Global Marketing & Communications Specialist for the Laboratory Enterprise Division (LED) in 2017. In 2018, he began his current role as product manager for Agilent's Relocation Services, part of Agilent’s enterprise offerings, in which he focuses on providing customers globally with improved business and science continuity throughout their relocation experiences.