Featured Article
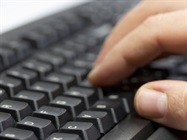
While advances in the metabolic and genetic engineering of E. coli bacterial strains have made it possible to produce a wide range of alternative biofuels through highly optimized, commercially viable processes,1 they present challenges involving quality control, production efficiency, and regulatory compliance, placing greater emphasis on efficient informatics and data management. Integrated solutions based on laboratory information management systems (LIMS) and chromatography data systems (CDS) help biofuel producers manage this complexity and ensure that processes are robust, safe, and efficient.
More data, less downtime
The genetically engineered microorganisms used in advanced biofuel production processes are more sensitive to environmental factors than the yeast-based fermentations used to produce ethanol from first-generation feedstocks. Toxic substances present in raw materials or generated during biomass pretreatment can inhibit fermentation, limiting process efficiency. Even small variations in temperature or pH can potentially kill bacteria. To minimize these risks, high-throughput analytical technologies such as near-infrared spectroscopy, gas chromatography, ion chromatography, liquid chromatography with charged aerosol detection or mass spectrometry and inductively coupled plasma mass spectrometry are used by biofuel producers to perform quality checks throughout production, from feedstock characterization and fermentation monitoring to end-product quality control. Many facilities use integrated LIMS and CDS to collect and manage the massive amounts of data generated. LIMS platforms that employ statistical quality control features, for instance, can apply advanced algorithms to identify and notify lab managers of results that fall outside acceptable limits. Quality issues can therefore be detected early.
With processes running 24/7, a key priority is ensuring the highest levels of instrument uptime. Proper and timely maintenance is critical: an underperforming instrument could compromise measurement data reliability and product quality. A faulty instrument could shut down the process entirely. When trended and analyzed, data such as baseline measurements, area counts, and retention times can be used to assess general instrument health. CDS and LIMS can be used to monitor equipment performance so that downtime can be planned as part of a regular maintenance schedule. Some CDS platforms allow instrument operation independent of the network, ensuring analytical sequences keep running and data is accessible for processing, even if unforeseen events such as network outages occur.
Robust processes produce reliable results
Biofuel producers are subject to regulatory and quality control requirements to ensure fuel quality and safety. ASTM D7862 dictates test methods and performance requirements for the blending of butanol with gasoline at levels of 1–12.5%. Water content, acidity, levels of inorganic chloride, sulfur, and sulfate must be monitored, and require a range of analytical techniques, each with its own standard operating procedure (SOP). These analyses involve complex and time-consuming sample and calibration standard preparation. Failure to properly implement SOPs for these tests can compromise data quality and regulatory compliance, potentially resulting in costly delays. In addition, each technique may require its own software package, which in turn necessitates analyst training. With an automated system running a LIMS and CDS capable of handling multiple chromatography techniques and instruments from a variety of vendors (and that includes quantitative MS capabilities), this complexity can be reduced significantly.
To perform chloride quantitation by ion chromatography, for example, with all the relevant method parameters needed for a chromatography protocol stored on a LIMS, a CDS with a built-in run execution system can download the protocol and initiate the analytical sequence. Not only does this save time, it also ensures that each analysis adheres to SOP requirements. In addition, LIMS can accelerate modification or addition of methods to a set of SOPs.
Some CDS platforms provide an even higher level of automation, extending to data processing and analysis. A CDS with intelligent run control parameters can enhance process efficiency by taking predefined actions based on run pass or fail criteria. The software can instruct the instrument to reinject samples, perform a dilution, or abort a run without user intervention. Eliminating the need to manually repeat measurements further boosts productivity and efficiency.
Conclusion
At the click of a button, integrated LIMS and CDS platforms can help operators recall information associated with a particular production process. Many CDS systems can automatically generate a detailed audit trail of all user actions, chromatographic run data, and conditions. Well-managed data has the potential to streamline processes, safeguard quality and ensure production is profitable.
Reference
- Koppolu, V. and Vasigala, V.K.R. Role of Escherichia coli in biofuel production. Microbiology Insights 2016; doi: 10.4137/MBI.S10878.
Barbara van Cann is product specialist, chromatography software, Thermo Fisher Scientific, Takkebijsters 1, 4817 BL Breda, The Netherlands; tel.: +31 76 579 5555; e-mail: [email protected]; www.thermofisher.com