Featured Article
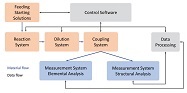
Online reaction monitoring systems (ORMS) are commonly used in process analytics in the chemical and pharmaceutical industries to determine the qualitative and quantitative composition of reactants, catalysts, and products. Several systems designed for special applications and processes are described in the literature and are commercially available.
There is an increasing demand for flexible, multiuse systems to monitor different applications and processes. In addition to qualitative and quantitative results, information about the molecular structure and elemental composition are required. To achieve this, measurement techniques with high sensitivity and selectivity must be integrated into the online system.
An online reaction monitoring system comprises several main components. The main part is the reaction system, e.g., a microreactor with different volumes. Connection between the reaction system and the measurement system is via a dedicated coupling system that allows the transfer of defined sample amounts to the analyzer. A dilution system can be integrated to adapt the concentration of the reaction solutions to the working range of the measurement device.
Microreactor systems
Chemical reaction systems in microscale are miniaturized systems with internal channels enabling continuous-flow reactions.1 The main fields of application of microscale reactors are the chemical and pharmaceutical industries, biotechnology, medicine, life sciences, clinical diagnostics, and environmental investigations.2 Due to their high mass and heat-transfer characteristics, microreactors reduce equipment size as well as materials and energy consumption.
Microreactors can be used at multiple locations with the possibility to integrate analytical instruments. Consequently, microreactors hold promise for use in online reaction monitoring systems, since fast data acquisition can be realized to view desired stages of the reaction process and are powerful tools in process analysis and optimization.3
Measurement techniques
Common measurement techniques applied in online reaction monitoring systems are spectroscopic methods such as ultraviolet/visible (UV/VIS), infrared (IR), fluorescence, Raman, X-ray fluorescence (XRF), and nuclear magnetic resonance (NMR).4 Electrospray ionization-mass spectrometry (ESI-MS) has been used for online monitoring of chemical and biochemical reactions.5,6 The literature shows that current online monitoring systems are designed for one or several types of reactions.
This article describes a mobile, modular ORMS with a continuous-flow reaction system that can be used for structural measurements using ESI-MS and for the determination of the elemental composition of reaction solutions using ICP-MS. System performance and accuracy were evaluated with standard solutions, compound mixtures, and model reactions.7-11
System concept and design
The ORMS consists of several subsystems: the feeding system that provides the starting solutions, the microreactor with an additional dilution system, the sampling system (coupling system), the measurement systems for structural and elemental analysis, and the software control system. Figure 1 gives a schematic overview of the ORMS structure and subsystems.
Figure 1 – ORMS structure and subsystems.Hardware
Feeding and reaction system
Two HPLC piston pumps—WellChrom K-501 and Smartline 100 (Knauer, Berlin, Germany)—are used to supply the starting solutions (educts) into the microreactor using a mixing valve. In general, microreactors of different designs can be used in the ORMS. The system presented operates with a modular meander microreaction system (Ehrfeldt Mikrotechnik, Wendelsheim, Germany) with a total volume of 11 mL. A refrigerated/ heating circulator (F26-HP, Julabo, Seelbach, Germany) ensures a constant reaction temperature from –20 °C (–4 °F) up to 200 °C (392 °F). Two Pt100 sensors were applied for temperature monitoring at the reactor inlet and outlet.
Dilution system
A G1968D mass rate attenuator (Agilent Technologies, Waldbronn, Germany) splits the flow between the reactor output and the dilution solvent. A WellChrom K-501 HPLC pump supplies the dilution solvent, and an additional HPLC pump (G1310A, Agilent Technologies) achieves the flow compensation in the case of low flow rates (<3 mL/min) from the microreactor output.9,11 The split factor varies the switching frequency (from 0.2 to 2 Hz) and aliquot volume (22, 100, and 300 nL). Thus, different flow rates and dilution ratios up to 1:100,000 can be attained. Typical values are 1:1,000, 1:500, 1:100, and 1:50.
Coupling and sampling system
An mzr-2942 microannular gear pump (HNP Mikrosysteme, Schwerin, Germany) provides a constant solvent supply to the measurement device. Liquid flow is controlled using a Coriolis miniCoryflow M13 flowmeter (Bronkhorst High-Tech B.V., Ruurlo, The Netherlands). Sampling is performed by a C10UW switching multiport valve (Vici, Schenkon, Switzerland) with a 5-µL sample loop. The sample from the reactor output/dilution module is injected into the solvent flow to the measurement system by switching the valve.
Measurement system
The ORMS can be connected to several mass spectrometers with atmospheric pressure ion sources. In this study, a G1969A time-of-flight mass spectrometer with electrospray ionization (ESI-MS) was used for structural compound monitoring and a 7700x ICP-MS was used for elemental monitoring (both from Agilent Technologies).
Software control
System data communication is performed using RS232 interfaces; USB interfaces are used between RS232 hubs and the control computer. The device software of the measurement instruments are MassHunter Acquisition and MassHunter Qualitative Analysis used for data acquisition and preprocessing in structural measurements and MassHunter Workstation for ICP-MS in elemental measurements (both from Agilent Technologies). ORMS control software (programmed in C++) is used for system operation and monitoring. As shown in Figure 2, the graphical user interface (GUI) is divided into three sections for each tab. The control section includes different tabs according to the modules and their functionalities (carrier solvent, manual and automated measuring, heater, dilution) for adjustment of the specific parameters. The status section shows the current parameters of the system components and the log section archives all system actions.
Figure 2 – ORMS control software GUI.Experimental
The ORMS provides different coupling modes and therefore the possibility to connect different measurement systems such as ESI-MS for structural and ICP-MS for elemental measurements. Since the ORMS has a mobile design, the system can be easily transported to the desired measurement system. Figure 3 shows a 3-D drawing of the ORMS coupled to the two mass spectrometers.
Figure 3 – ORMS coupling to ESI-MS and ICP-MS.Structural monitoring
The ORMS enables monitoring of the amount of educts, products, and internal standards during chemical reactions. Two sampling methods are available for various applications (see Table 1): the slow sampling method (SSM) is used for replicate measurements of the desired reaction state, and the fast sampling method (FSM) enables rapid and material saving single measurements. The high concentration of reactants was reduced to the working range of the mass spectrometer using the additional dilution module. System performance was evaluated using defined standard solutions and chemical reactions, such as the monitoring the acetylation of tryptophan. Detailed results can be found in Refs. 7–9.
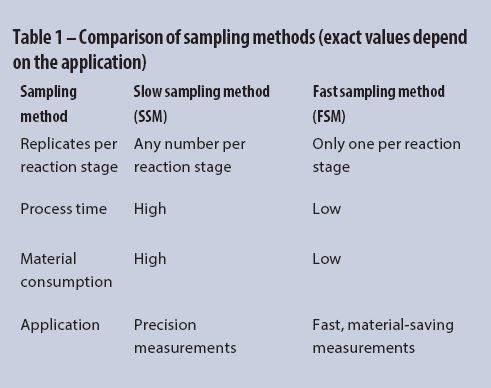
Elemental monitoring
To enhance method scope, the ORMS can be coupled to an ICP-MS for elemental analysis. This is a promising approach, particularly in catalyst-based reactions to monitor catalyst conversion. Two coupling concepts were developed and used, depending on the desired measurement mode. In spectrum analysis, the samples are measured in short time frames (approx. 2 min); in time-resolved analysis, time-dependent measurement signals are acquired (see Table 2). The concentration of the reaction solutions is adjusted to the ICP-MS working range using the dilution system. System performance was evaluated using standard elemental solutions. The current system setup is limited due to the metal parts of the microreactor and the microannular gear pump for carrier solvent supply. The reaction solution is contaminated by copper and iron. For reliable measurements of these elements, the materials of the affected system components should be changed.10,11
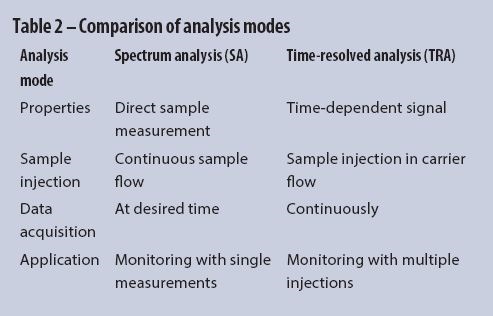
Summary and outlook
Effective monitoring of chemical reactions is achieved with the flexible, mobile ORMS presented here. The system consists of a tempered microreactor with an additional online dilution system. Depending on the application, the system can be coupled to a high-resolution ESI-MS for structural analysis and to an ICP-MS for elemental analysis. Several sampling and analysis modes are available. The ORMS and measurement devices are software controlled. Comfortable adjustment of the reaction and measurement parameters is afforded by the GUI. Future developments include extending the software for automated data processing and evaluation.12,13 Notably, the combination of the results of structural and elemental measurements will increase the information content.14-16
References
- Borovinskaya, E.S.; Reshetilovskii, V.P. Russ. J. Appl. Chem. 2008, 81(12), 2211–31.
- Šalić, A.; Tušek, A. et al. J. Appl. Biomed. 2012, 10(3), 137–53.
- McMullen, J.P.; Jensen, K.F. Ann. Rev. Anal. Chem. 2010, 3(1), 19–42.
- Yue, J.; Schouten, J.C. et al. Ind. Eng. Chem. Res. 2012, 51(45), 14,583–609.
- Zhu, Z.; Bartmess, J.E. et al. Anal.Chem. 2012, 84(17), 7547–54.
- Santos, L.S. J. Braz. Chem. Soc. 2011, 22(10), 1827–40.
- Fleischer, H.; Hoffmann, D. et al. IEEE International Instrumentation and Measurement Technology Conference (IEEE I2MTC) 2015, 1561–6.
- Do, V.Q.; Hoffmann, D. et al. ACECS 2016, 528–34.
- Do, V.Q.; Fleischer, H. et al. Am. Lab. 2017, 49(1), 36–40.
- Do, V.Q.; Ramani, K. et al. IEEE I2MTC 2017, 1375–80.
- Do, V.Q.; Fleischer, H. et al. IEEE I2MTC 2018, 1625–30.
- Fleischer, H.; Adam, M. et al. IEEE I2MTC 2015, 1602–7.
- Fleischer, H.; Adam, M. et al. IEEE CASE 2015, 758–63.
- Adam, M.; Fleischer, H. et al. 21st IMEKO TC-4 2016, 278-83.
- Adam, M.; Fleischer, H. et al. SLAS Technol. 2017, 22(2), 186–94.
- Adam, M.; Fleischer, H. et al. IEEE I2MTC 2017, 1381–6.
Heidi Fleischer, Ph.D., is university lecturer at the University of Rostock, Institute of Automation, Richard-Wagner-Strasse 31, 18119 Rostock, Germany; tel.: +49 (0) 381 498 7803; fax: +49 (0) 381 498 7802; e-mail: [email protected]; www.uni-rostock.de. Vinh Quang Do, Ph.D., is with the University of Rostock, Institute of Automation. Kerstin Thurow, Ph.D., is CEO of the Center for Life Science Automation—celisca, Rostock, Germany. The authors wish to thank the Federal Ministry of Education and Research Germany (FKZ: 03Z1KN11) and the Vietnam Ministry of Education and Training for the Project 911 Scholarship for financial support of this project.